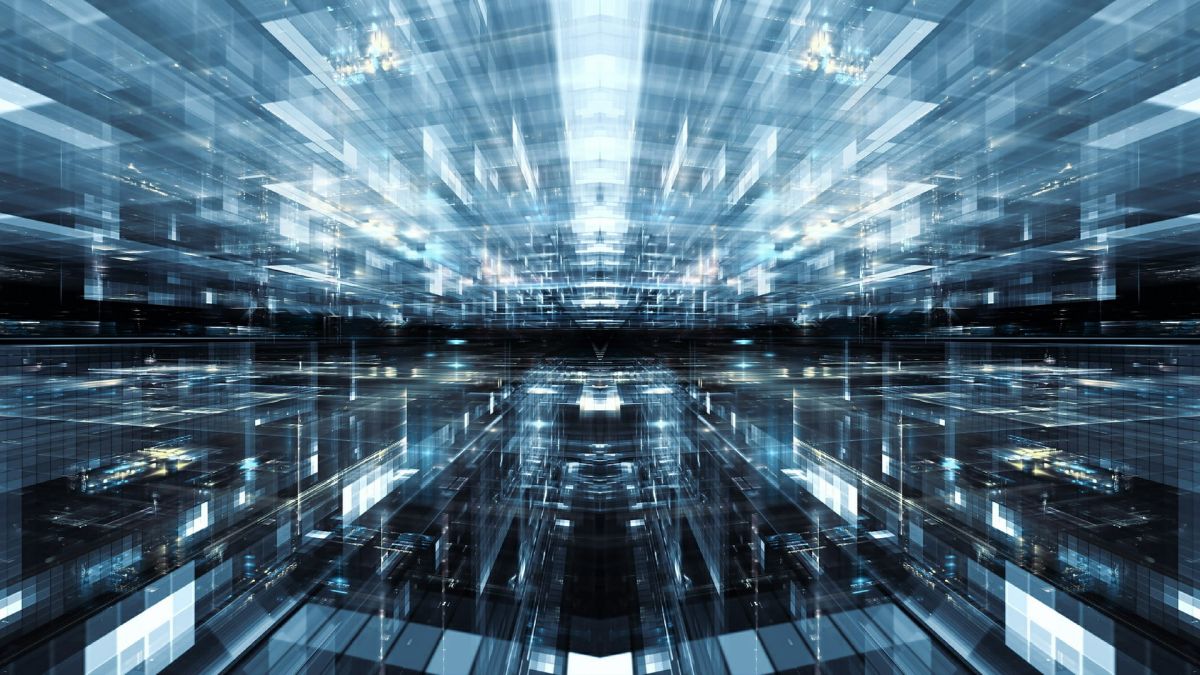
Gli stabilimenti di produzione giapponesi della Toyota sfornano circa 13.500 nuovi veicoli al giorno, ma l’anno scorso, 14 stabilimenti sono stati messi offline per 24 ore a causa di un singolo problema software. In Australia, un impianto di gas naturale della Chevron è andato offline per riparazioni non pianificate, facendo salire i prezzi globali dell’energia. E quando il plating equipment ha preso fuoco in una fabbrica di semiconduttori della Renesas, ci sono voluti mesi per ripristinare la produzione, costando all’azienda 156 milioni di dollari al mese.
Questa è la realtà della produzione moderna: gli impianti industriali sono incredibilmente sofisticati, ma possono essere messi offline da un singolo guasto in qualsiasi punto della catena di montaggio. La quantità esatta di denaro persa, quando questo accade, varia a seconda del settore, da $36.000 all’ora nel settore dei beni di consumo in rapida evoluzione ad una media di $125.000 all’ora nei settori dell’energia e dell’industria pesante. Gli esperti stimano che i tempi di inattività non pianificati costino alle più grandi aziende del mondo più di $1,4 trilioni all’anno .
La manutenzione programmata può aiutare a far funzionare senza problemi gli impianti. Ma per ridurre i tempi di fermo non pianificati, dobbiamo andare oltre e unire i puntini tra gli operatori degli impianti e i produttori di apparecchiature. Con una migliore comunicazione tra queste parti interessate, con una produzione realmente connessa, abbiamo l’opportunità di risolvere questo problema da un trilione di dollari e migliorare radicalmente lo status quo.
Negli impianti di produzione odierni, quando un motore si blocca, la catena di montaggio si ferma. I lavoratori eseguono le riparazioni e le cose tornano a funzionare correttamente, fino alla volta successiva. Nessuno sta realmente monitorando il motivo per cui il motore si è rotto o sta lavorando per capire la causa principale del problema; stanno solo reagendo ai guasti man mano che si verificano.
E se ci fosse un modo migliore? Immagina un mondo in cui quel motore invia continuamente dati operativi al produttore dell’attrezzatura originale (Original Equipment Manufacturer), dandogli visibilità sulle sue prestazioni. Quando il motore inizia a surriscaldarsi, l’OEM può avvisare in modo proattivo l’operatore dell’impianto prima che si verifichi un’interruzione importante.
Consolidando le capacità di monitoraggio delle apparecchiature, gli OEM (Original Equipment Manufacturer) possono accelerare il ciclo di innovazione per sviluppare apparecchiature di nuova generazione con prestazioni e affidabilità superiori. Ciò è particolarmente importante man mano che l’intelligenza artificiale si fa avanti: solo gli OEM in grado di acquisire e compilare dati sulle prestazioni del mondo reale saranno in grado di addestrare modelli e creare macchinari più intelligenti per ottenere vantaggi per gli utenti finali.
Infine, la condivisione dei dati favorisce una partnership più forte tra OEM e operatori di stabilimento, focalizzata sulla fornitura di valore e risultati garantiti, piuttosto che sulle vendite di apparecchiature transazionali. Rolls-Royce ha aperto la strada a questo approccio con power-by-the-hour per le compagnie aeree (in pratica i proprietari degli aerei pagano la Rolls Royce solo per le ore di volo in cui i motori dell’aereo sono in uso); con una migliore connettività, potrebbe diventare lo status quo anche nella produzione. Il risultato finale sarebbe una relazione più profonda tra OEM e stabilimenti, e maggiori ricavi per tutti.
Abbiamo già la tecnologia necessaria per attuare questa visione. La maggior parte delle fabbriche è gestita attraverso gemelli digitali, con macchinari che comunicano il proprio stato ad hub locali in tempo reale; pertanto, si tratta semplicemente di inviare questi dati agli OEM. È semplice, vero?
Bene, non così rapidamente. Per realizzare una produzione connessa, dovremo affrontare quattro sfide principali:
1. Semplicità
Se ogni macchinario fosse fornito da un unico produttore di attrezzature OEM, la produzione sarebbe estremamente semplice. Tuttavia, la realtà è che anche un’operazione apparentemente semplice come la preparazione di patatine fritte può necessitare di oltre mezza dozzina di macchine differenti per mescolare, impastare, tagliare, gestire gli scarti, friggere, selezionare, insaporire e imballare il prodotto finale.
Il risultato è spesso un complesso assemblaggio alla Rube Goldberg di attrezzature di vari OEM (una macchina di Rube Goldberg è un dispositivo intenzionalmente intricato per svolgere compiti semplici). Non è realistico aspettarsi che i produttori gestiscano la loro linea di assemblaggio con decine di app differenti dagli OEM. Ciò di cui abbiamo bisogno è un unico strato unificatore integrato nel gemello digitale dell’impianto, che assicuri interoperabilità e scambio di informazioni tra il punto di utilizzo e l’OEM.
2. Riservatezza
Per i produttori i dati operativi sono di natura commerciale sensibile. Le relazioni con i clienti potrebbero essere compromesse se informazioni come progetti, specifiche e dettagli degli ordini vengono rivelate, così come la divulgazione di dettagli sull’efficienza operativa o indicatori di prestazione (KPI) possono svantaggiare le aziende sul mercato. Attualmente, il costo medio di una violazione dei dati per i produttori è di 5,56 milioni di dollari. (vedi Report 2024 Cost of a Data Breach – IBM).
Con l’aumento dell’attenzione normativa sulla privacy dei dati, spinta dal Regolamento Generale sulla Protezione dei Dati (GDPR) europeo e dalle leggi statunitensi, è evidente che la privacy dei dati diventerà una priorità imprescindibile per i produttori. Se esiste il rischio di una fuga di dati verso terze parti, gli operatori degli impianti potrebbero rifiutarsi di adottare la produzione connessa.
3. Sicurezza
Gli impianti di produzione moderni, che dipendono da sistemi IoT distribuiti e sono suscettibili a dispendiosi fermi macchina se un singolo dispositivo viene disconnesso, rappresentano obiettivi primari per gli attacchi ransomware. Nel solo 2024, gli hacker hanno provocato gravi disfunzioni, inclusi arresti totali degli impianti, in più di 500 siti industriali.
Di conseguenza, i produttori sono giustamente prudenti nel non ampliare la superficie di attacco per gli hacker. Per essere efficace, la produzione connessa richiede una sicurezza impenetrabile, preferibilmente sfruttando le pipeline di dati esistenti piuttosto che creare nuovi punti di accesso in apparecchiature industriali fondamentali.
4. Il cliente al primo posto
Il successo della produzione connessa dipenderà dalla sua capacità di fornire un valore tangibile ai clienti. Non dobbiamo ripetere gli errori di altre aziende, che hanno creato dispositivi connessi limitando la libertà di riparazione o l’uso flessibile dei macchinari per raggiungere obiettivi specifici.
Al contrario, gli OEM devono puntare costantemente a offrire maggior valore e a stabilire relazioni più forti con gli operatori degli impianti. I produttori non dovrebbero mai interrogarsi sul proprio guadagno; i benefici della produzione connessa devono essere chiari e indiscutibili per garantire l’adesione.
Colmare il divario
Le sfide persistono mentre ci avviciniamo all’avvio di una nuova era di produzione interconnessa. Tuttavia, queste difficoltà sono superabili e i benefici potenziali, sia per gli operatori degli impianti che per gli OEM, sono notevoli.
L’industria manifatturiera è al cospetto di una trasformazione radicale, con la condivisione di dati in tempo reale che sta ridefinendo le dinamiche tra produttori e fornitori di apparecchiature OEM. Superando queste barriere, si apre la possibilità di rivoluzionare il settore manifatturiero, incrementando la resilienza e la profittabilità per gli operatori di impianti di vario genere e permettendo agli OEM di spingere sull’acceleratore dell’innovazione e di forgiare legami più solidi e duraturi con i loro clienti.