Aumenta l’efficienza e riduci gli sprechi con le Procedure Operative Standard Lean
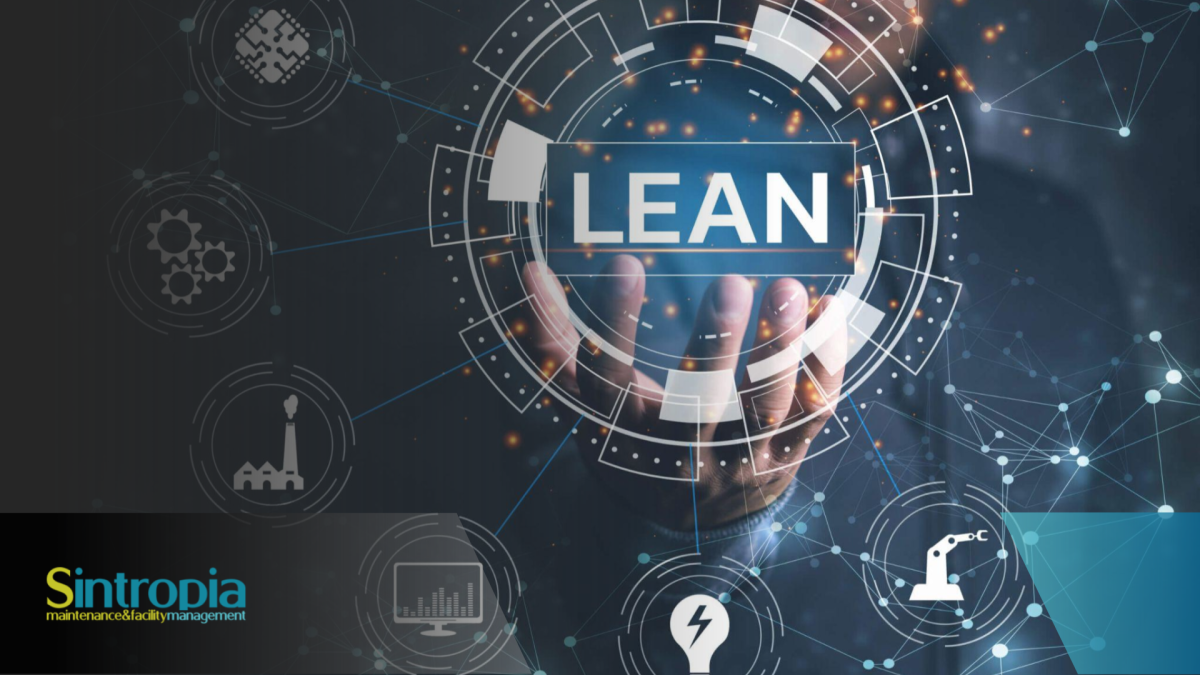
Le strategie Lean si concentrano sull’eliminazione degli sprechi in termini di tempo, sforzi e risorse, massimizzando al contempo l’efficienza delle operazioni.
La tua azienda può ottimizzare sia il tempo che il denaro adottando una strategia Lean, raggiungendo al contempo livelli di performance superiori. Le strategie Lean si focalizzano sull’eliminazione dei sprechi in termini di tempo, sforzi e risorse, per massimizzare l’efficienza operativa. Quando si tratta di SOP per la manutenzione preventiva, è essenziale assicurarsi che ogni passaggio sia necessario, pertinente ed efficace, per prevenire eventuali problemi o guasti prima che si verifichino.
Che cosa è Lean?
Le strategie Lean sono un insieme di principi e approcci aziendali volti a minimizzare costi, tempi e risorse, ottimizzando al contempo il valore complessivo dei risultati. Questo processo avviene attraverso l’eliminazione di elementi non necessari o ridondanti, come sovrapproduzione, accumulo di scorte, tempi di attesa e movimenti extra.
Questo approccio, noto come “produzione snella”, è stato introdotto da Toyota alla fine degli anni ’80 per semplificare i processi di produzione e ridurre gli sprechi.
Le strategie Lean si concentrano sull’identificazione e l’eliminazione delle attività che non aggiungono valore, semplificando i processi e trovando modi per ottenere più valore con meno risorse. Queste strategie si focalizzano sul flusso di produzione, sul feedback dei clienti e sull’ottimizzazione del sistema, creando operazioni più snelle ed efficienti sia in officina che sul campo.
Ben noto nel settore manifatturiero, la Lean si riferisce a metodi che aiutano a identificare ed eliminare gli sprechi operativi; Six Sigma si riferisce a tecniche utilizzate per migliorare i processi e la qualità. La metodologia Six Sigma include cinque passaggi chiave: definire, misurare, analizzare, migliorare e controllare (DMAIC). Forbes
Un elemento essenziale delle strategie Lean è l’approccio “Kaizen”, che prevede il miglioramento continuo in tutte le aree della tua azienda. Ciò significa che i team dovrebbero valutare costantemente i loro processi per identificare cosa può essere migliorato o eliminato del tutto. Altri strumenti Lean che la gestione delle operazioni potrebbe trovare utili includono il Gemba Walk, il Lean Six Sigma e altri sistemi di gestione finalizzati alla riduzione degli sprechi.
Che cosa sono i DOWNTIME?
Nel mondo della produzione, il termine downtime si riferisce alla quantità di tempo in cui la produzione si ferma a causa di apparecchiature non funzionanti. Tuttavia, i downtime possono anche rappresentare tempo sprecato all’interno del ciclo di produzione della tua azienda.
Puoi utilizzare la metodologia DOWNTIME, un acronimo che indica otto categorie di spreco da eliminare, per diventare più efficienti:
- Difetti: Correggere errori di produzione (Defects)
- Sovrapproduzione: Produrre solo quanto richiesto (Overproduction)
- Attesa: Ridurre i tempi morti tra le operazioni (Waiting)
- Non utilizzo dei talenti: Massimizzare le competenze del personale (Not utilizing talent)
- Trasporti: Ottimizzare i movimenti dei materiali (Transportation)
- Inventario eccessivo: Mantenere livelli di scorte ottimali (Inventory excess)
- Sprechi di movimento: Minimizzare i movimenti inutili dei lavoratori (Motion waste)
- Elaborazione eccessiva: Eliminare passaggi non necessari nel processo (Excess processing)
Quali sono i vantaggi della Lean?
Le aziende spesso adottano approcci Kaizen, come il benchmarking rispetto ai concorrenti o agli standard di settore, la sperimentazione di nuove tecnologie o processi, l’analisi delle cause profonde delle inefficienze e il processo decisionale basato sui dati.
Inizia identificando le aree di potenziale miglioramento nei processi o prodotti esistenti della tua azienda. Puoi individuare queste carenze utilizzando tecniche di analisi dei dati come la mappatura del flusso di valore, che schematizza ogni passaggio di un processo per individuare opportunità di ottimizzazione o semplificazione.
La riprogettazione dei processi Lean consente alle aziende di semplificare le operazioni, eliminare gli sprechi e promuovere una cultura di miglioramento continuo. Questa metodologia versatile si applica efficacemente ai processi a ciclo breve e a ciclo lungo, ai processi transazionali e decisionali, nonché ai processi rivolti al cliente e interni. McKinsey
Una volta identificate queste aree, puoi implementare soluzioni di standardizzazione per affrontarle, come l’introduzione dell’automazione nelle attività ripetitive o la modifica della progettazione di prodotti o servizi per aumentare la soddisfazione del cliente.
Inoltre, è essenziale creare una cultura di miglioramento continuo tra i dipendenti affinché i benefici delle strategie Lean siano massimizzati nel tempo. Questo implica cercare feedback regolari dai clienti sulle loro esigenze e aspettative e mantenere una comunicazione aperta tra i diversi reparti della tua azienda sulle best practice per l’efficienza e il risparmio dei costi.
Perché utilizzare un approccio Lean per scrivere le Procedure Operative Standard?
Utilizzare strategie Lean per redigere istruzioni di lavoro sotto forma di Procedure Operative Standard (SOP) può migliorare significativamente l’efficacia del tuo team di manutenzione. Per massimizzare l’efficacia delle SOP di manutenzione preventiva seguendo una strategia Lean, prova a seguire questi suggerimenti:
- Attività a valore aggiunto: Concentrati sulle attività che contribuiscono direttamente a mantenere le prestazioni ottimali all’interno dell’azienda. La metodologia Lean suggerisce di identificare i processi da migliorare o eliminare per ridurre gli sprechi e ottimizzare l’uso delle risorse.
- Mappatura del flusso di valore (Value Stream Mapping): Crea una rappresentazione visiva, come un diagramma di flusso, di tutti i passaggi necessari per completare un’attività o un processo, dal suo inizio alla sua conclusione. Le iniziative VSM aiutano a identificare le aree in cui gli sforzi duplicati o i passaggi non necessari possono essere eliminati o combinati per migliorare l’efficienza e ridurre gli sprechi.
- Analisi dei processi: Esamina attentamente i processi esistenti per identificare eventuali aree di inefficienza o spreco. Adatta il processo passo dopo passo, il più possibile, con un impatto minimo sui livelli di performance complessivi. Questo include l’analisi delle risorse, dei flussi di lavoro, degli strumenti, delle attrezzature utilizzate, delle procedure seguite, dei requisiti di onboarding e formazione, e altro ancora.
- Checklist: Redigi checklist per le attività comprese nelle SOP di manutenzione preventiva, assicurandoti che vengano eseguite sempre in modo coerente, corretto ed efficiente. Questo riduce la probabilità di errori operativi e garantisce un livello di qualità costante nei processi aziendali.
- Miglioramento continuo: Assicurati di rivedere e migliorare costantemente le procedure operative standard di manutenzione preventiva, apportando modifiche e miglioramenti per aumentare ulteriormente l’efficienza.
Come utilizzare un approccio Lean SOP
L’adozione di un approccio snello nella redazione di procedure operative standard efficaci per la manutenzione preventiva può portare alla tua azienda diversi benefici, tra cui:
- Maggiore produttività, grazie a flussi di lavoro ottimizzati.
- Riduzione dei costi, attraverso un utilizzo più efficiente delle risorse.
- Maggiore precisione, mediante l’impiego di checklist strutturate.
- Qualità superiore, garantita da aggiornamenti e revisioni frequenti.
Seguendo una strategia snella nella creazione delle procedure operative standard (SOP) per la manutenzione preventiva, la tua azienda avrà l’opportunità di ottimizzare l’efficienza operativa e minimizzare gli sprechi.
Le strategie lean possono apportare numerosi vantaggi, come la riduzione dei costi operativi e il miglioramento della qualità dell’output, senza compromettere la soddisfazione del cliente o gli standard di sicurezza. Adottando con successo questi principi, le aziende possono ottenere una maggiore produttività, esperienze più soddisfacenti per i clienti, tempi di consegna più brevi, minori livelli di inventario e costi inferiori nella produzione di beni o servizi, mantenendo al contempo la competitività nell’attuale mercato.
Per concludere, implementa cicli di feedback per individuare rapidamente i problemi e affrontarli in modo adeguato. La tua azienda dovrebbe raccogliere costantemente informazioni sui clienti attraverso sondaggi o interviste, consentendo di comprendere a fondo le loro necessità e preferenze. Questo approccio facilita la creazione di prodotti o servizi che rispondano meglio alle loro aspettative. Inoltre, adotta sistemi automatizzati per monitorare i reclami dei clienti e avvisare tempestivamente il team in caso di anomalie, consentendo di intervenire prontamente e prevenire problemi più gravi.
Come creare procedure operative standard snelle
Redigere procedure operative standard (SOP) efficaci per la manutenzione preventiva è cruciale per le aziende che dipendono dall’utilizzo di macchinari, sistemi o altre apparecchiature.
Adottare una strategia snella durante la redazione di queste SOP contribuisce a garantire processi efficienti e completi. Per realizzare procedure operative standard, è importante che la tua SOP sia digitale, integrata e interattiva.
Le SOP in formato digitale garantiscono a tutti i membri del team l’accesso immediato agli aggiornamenti in tempo reale, contribuendo a risparmiare tempo. Inoltre, permettono di integrare istruzioni dettagliate con il supporto di video e immagini. Sebbene non esista un unico formato standard per le SOP, l’utilizzo di un modello digitale facilita la creazione e l’aggiornamento delle procedure, rendendo il processo molto più rapido. Un modello standardizzato consente, inoltre, agli utenti di individuare facilmente le informazioni necessarie.
Un documento interattivo di procedura operativa standard (SOP) offre ai dipendenti una checklist o un modello pratico. I passaggi vengono visualizzati uno alla volta durante l’esecuzione e possono essere spuntati man mano che vengono completati. Questo approccio è particolarmente utile per l’inserimento di nuovi dipendenti. Una SOP integrata, invece, sfrutta l’automazione per semplificare le attività. Inserendo i dati nel modello, i dipendenti possono attivare ulteriori passaggi in base alle esigenze. È anche possibile generare report, inclusi diagrammi di flusso, per monitorare le prestazioni, i tempi di inattività e l’inventario. In questo modo, la nuova SOP diventa un’applicazione interattiva piuttosto che un semplice manuale.
Cosa dovrebbero includere le tue procedure operative standard (SOP) Lean?
Per organizzare al meglio le tue procedure operative standard, puoi seguire il modello SOP descritto di seguito:
- Intestazione: Include il nome dell’attività, il numero ID della SOP, la data di creazione o l’aggiornamento, la posizione in cui la procedura operativa standard è applicabile e i nominativi delle parti interessate che hanno contribuito alla sua redazione.
- Revisione: Riporta la cronologia delle revisioni, specificando le date di creazione e gli eventuali aggiornamenti.
- Sommario: Riassume il contenuto del documento e aiuta i lavoratori a trovare il punto di partenza.
- Scopo della SOP: Elenca tutte le procedure incluse nella SOP.
- Ruoli e responsabilità: Indica i lavoratori che seguiranno la procedura operativa standard. Quando identifichi un team, tieni presente che di solito include project management, operations manager, maintenance manager e altri dipendenti. Questo evita le incomprensioni.
- Procedura: Contiene istruzioni essenziali passo dopo passo. Qui è dove si delineano le attività specifiche.
- Informazioni aggiuntive: Elenca i dettagli sulla salute e sulla sicurezza, compresi i dispositivi di protezione necessari. Include le normative del settore e i materiali di formazione o le guide necessarie.
- Glossario: Definisce i termini e gli acronimi utilizzati nelle procedure operative standard.
- Approvazione: Fornisce lo spazio per le firme di approvazione della procedura standard.
Come rivedere i tuoi Lean SOPS
Una volta terminata la prima bozza, chiedi a chi svolge il lavoro di rivederla per verificarne l’accuratezza e la completezza. Coinvolgere le parti interessate è essenziale. Ottenere input da coloro che utilizzeranno la procedura, assicura che i suoi passaggi abbiano senso dal loro punto di vista. Inoltre, conferisce loro la responsabilità del suo successo o fallimento, il che potrebbe portare a ulteriori miglioramenti se necessario. Inoltre, i dipendenti sono valorizzati quando la direzione riconosce le loro competenze e conoscenze. Ciò spesso porta ad una soddisfazione sul lavoro e a tassi di turnover più bassi.
Riconoscere le Competenze dei Dipendenti:
- La direzione deve riconoscere le competenze e le conoscenze dei dipendenti.
- Questo rafforza il loro impegno e spesso porta a una maggiore soddisfazione sul lavoro e a tassi di turnover più bassi.
Verifiche e Conflitti:
- Chiedi ai revisori di verificare se i passaggi della SOP si sovrappongono ad altre procedure o vanno in conflitto con le normative esistenti.
Formazione Continua:
- Forma continuamente il personale responsabile delle attività di manutenzione preventiva.
- Fornisci nuovi materiali di formazione insieme ai nuovi documenti SOP per garantire che tutti comprendano i propri ruoli e come affrontare ogni attività.
- Questo è particolarmente importante per i nuovi dipendenti che potrebbero aver bisogno di assistenza nella risoluzione dei problemi.
Integrazione delle SOP nel Sistema:
- Considera come le SOP si integrano in un sistema coeso.
- Adotta una visione olistica dell’intero sistema invece di concentrarti solo su singoli macchinari o attrezzature.
- Questo ti permetterà di individuare aree di sovrapposizione o ridondanza, migliorando l’efficienza complessiva.
Misurazione delle Prestazioni:
- Misura le prestazioni delle SOP tramite indicatori chiave di prestazione (KPI) per valutare i progressi rispetto agli obiettivi.
- Identifica le aree di ulteriore miglioramento.
Revisione Annuale:
- Rivedi regolarmente ciascuna sezione del documento, almeno una volta all’anno, per garantirne l’accuratezza e la pertinenza.
Utilizzare un CMMS per migliorare le procedure operative standard
Un sistema di gestione della manutenzione computerizzata (CMMS) è uno strumento prezioso per migliorare l’efficienza e l’efficacia delle attività di manutenzione pianificate. Utilizzando una piattaforma centralizzata per gestire e monitorare queste attività, un CMMS riduce il rischio di errori. Inoltre, migliora la comunicazione e il coordinamento tra i membri del team e ottimizza l’uso delle risorse.
Automatizzare la pianificazione e monitorare i progressi.
Un vantaggio fondamentale dell’utilizzo di un CMMS è che consente di pianificare e monitorare le attività di manutenzione e riparazione in tempo reale. Può anche migliorare la tenuta dei registri e la documentazione delle attività di manutenzione, risultando inestimabile durante le ispezioni per scopi di conformità e normativi. Inoltre, un CMMS offre facili integrazioni con le tue soluzioni software aziendali EAM, EAP e altre, in tutti i settori.
Migliorare la comunicazione e la collaborazione
Un CMMS può migliorare la comunicazione e il coordinamento tra i membri del team. Ogni membro coinvolto in un compito specifico sarà consapevole delle proprie responsabilità e dello stato del lavoro svolto.
Ottimizzare le risorse
Un CMMS può ottimizzare l’uso delle risorse, incluse attrezzature, pezzi di ricambio, strutture e personale. Fornendo dati e analisi in tempo reale sullo stato delle attività di manutenzione, un CMMS aiuta a ridurre i costi, gestire le sfide della supply chain e integrare strategie di manutenzione snella.