KPI in azione: esempi reali di manutenzione e produzione
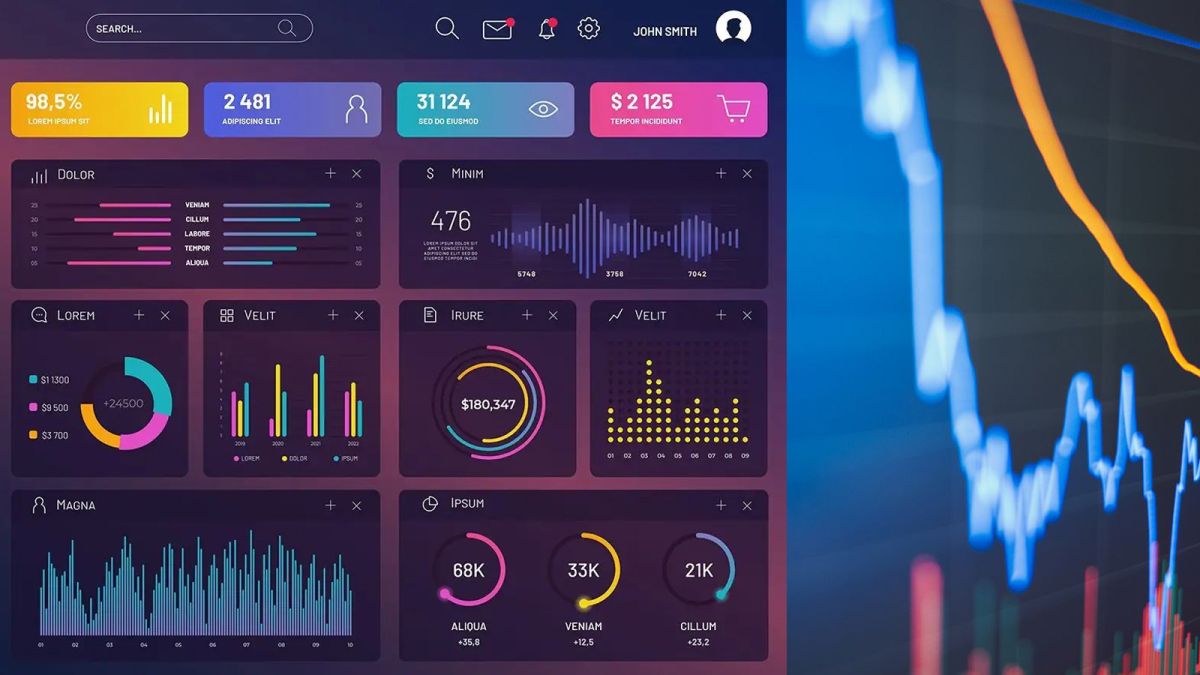
Non è possibile migliorare ciò che non si misura, ma nel panorama dinamico della manutenzione e della produzione è anche importante selezionare le cose giuste da misurare. Per anni c’è stata la tendenza a tenere traccia di cose come il numero di ordini di lavoro completati, che in realtà hanno ben poco impatto sulla salute delle risorse e sul successo aziendale.
La gestione delle operazioni sugli asset, d’altro canto, incoraggia la selezione di quegli indicatori prestazionali (Key Performance Indicator) che hanno un collegamento diretto con gli scopi, gli obiettivi e la strategia dell’impresa. Questi parametri dovrebbero concentrarsi sulla riduzione dei tempi di inattività, sull’aumento della produttività e sulla diminuzione dei tassi di guasto delle apparecchiature. Osservando questi KPI, possiamo elevare la manutenzione dall’essere un centro di costo strettamente non apprezzato ad un partner prezioso nella generazione di entrate all’interno delle nostre organizzazioni.
La selezione dei giusti indicatori prestazionali è fondamentale per aiutare i produttori a semplificare le attività di manutenzione, dare priorità alle riparazioni sulle risorse critiche e collegare le proprie attività agli obiettivi aziendali. Le aziende che selezionano gli indicatori in grado di ridurre i tempi di inattività possono aumentare con successo la produttività delle proprie operazioni, migliorare la redditività e aumentare la soddisfazione del cliente.
Le seguenti metriche forniscono informazioni preziose sullo stato delle risorse, sull’efficacia delle strategie di manutenzione e sulle prestazioni complessive dei team di manutenzione.
Overall Equipment Effectiveness (Efficacia complessiva delle apparecchiature)
L’OEE è un parametro completo che valuta l’efficienza dell’utilizzo delle apparecchiature esaminando la disponibilità, le prestazioni e la qualità di una risorsa in un determinato periodo di tempo. Misurando l’OEE, i produttori possono identificare le aree di miglioramento, come la riduzione dei tempi di inattività, l’aumento dei tassi di produzione e il miglioramento della qualità del prodotto. Un punteggio OEE perfetto implica che un’attrezzatura o una linea di produzione produce parti di alta qualità il più velocemente possibile senza fermarsi.
Quando uno di questi tre fattori non è ottimizzato, un’azienda può individuare e definire meglio le priorità di manutenzione.
La formula per determinare l’OEE è: OEE = disponibilità x prestazioni x qualità.
L’OEE è uno dei migliori KPI da utilizzare nella manutenzione e nella produzione, che si basa su disponibilità, prestazioni e qualità.
Consideriamo un produttore di componenti automobilistici che lavora su un turno al giorno. Il calcolo dell’OEE inizia con la valutazione della disponibilità. Il tempo di produzione pianificato, ovvero il tempo massimo di funzionamento delle apparecchiature, tiene conto della disposizione dei turni, delle pause e del pranzo. Il nostro produttore ha un tempo di produzione pianificato di 400 minuti al giorno. Il tempo di esecuzione effettivo prende quindi in considerazione sia i tempi di inattività pianificati che quelli non pianificati. Supponiamo che in questo esempio il produttore abbia 50 minuti di inattività al giorno, per un tempo di esecuzione di 350 minuti. La disponibilità equivale al tempo di esecuzione diviso per il tempo di produzione pianificato, che nel nostro esempio è pari all’87,5%.
Il secondo fattore nell’OEE è la prestazione, che esamina le prestazioni effettive dell’asset rispetto alla sua capacità ottimale. Ad esempio, se la risorsa ha un tempo di ciclo ideale di un secondo e può produrre 20.000 pezzi al giorno, se moltiplichi questi numeri e li dividi per il tempo di esecuzione calcolato in secondi, ottieni un fattore di prestazione di circa il 95%.
Infine, l’OEE guarda alla qualità. Per misurare la qualità, questo produttore deve sapere quante parti vengono scartate ogni giorno. Se su 20.000 pezzi 2.000 vengono rifiutati, la misura della qualità corrisponde al 90%.
L’OEE viene quindi calcolato moltiplicando disponibilità, prestazioni e qualità. In questo caso il produttore di componenti automobilistici ha un OEE di circa il 75%. Per migliorare l’OEE, questo produttore di componenti automobilistici potrebbe voler analizzare il motivo per cui ogni giorno vengono scartati 2.000 componenti, per migliorare la qualità o implementare pratiche di manutenzione per ridurre i tempi di fermo pianificati e non pianificati.
Mean Time Between Failures (Tempo medio tra i guasti)
L’MTBF è il tempo medio di funzionamento di un’apparecchiatura prima di subire un guasto o un guasto del sistema. Comprendere l’MTBF è fondamentale per garantire le prestazioni, la sicurezza e la progettazione delle apparecchiature delle risorse critiche. Quantificando la probabilità che un’apparecchiatura o un componente si guasti entro un determinato periodo di tempo, le aziende possono valutare meglio l’affidabilità dei sistemi che supportano le operazioni aziendali complessive.
La formula per determinare l’MTBF è: MTBF = ore di funzionamento totali dell’asset/numero totale di guasti dell’asset.
L’MTBF aiuta le aziende a misurare la probabilità che un asset o un componente di un asset si guasti entro un determinato periodo di tempo. Un MTBF elevato spesso significa maggiore affidabilità, mentre uno inferiore può indicare potenziali spese per più guasti. Una volta che un produttore calcola questa misura, può prendere in considerazione miglioramenti dei processi, standardizzazione dei dati e il root cause analysis per migliorare l’MTBF.
Ad esempio, un’azienda di confezionamento alimentare ha una macchina che funziona 8 ore al giorno e nel corso di un mese si guasta tre volte in 20 giorni lavorativi . Per facilità di calcolo, supponiamo che i guasti si verifichino ciascuno dopo un’intera settimana lavorativa e ciascuno richieda due ore per essere riparato. L’MTBF è pari a (40 ore + 38 ore + 38 ore + 38 ore) diviso per tre suddivisioni, ovvero un MTBF di circa 51,3 ore.
Per aumentare l’MTBF, questa azienda di imballaggio potrebbe prendere in considerazione il monitoraggio basato sulle condizioni, utilizzando sensori che potrebbero indicare un guasto imminente o implementare ispezioni di manutenzione preventiva su base settimanale, per ridurre potenzialmente il numero di guasti. Potrebbe anche eseguire un’analisi delle cause principali, per determinare esattamente il motivo per cui l’asset si guasta su base quasi settimanale.
Mean Time to Repair (Tempo medio di riparazione)
In relazione all’MTBF, l’MTTR misura il tempo medio necessario per ripristinare lo stato operativo delle apparecchiature danneggiate. Quanto più tempo è necessario per riparare un bene, tanto maggiori saranno i tempi di inattività e i relativi costi. Osservare l’MTTR aiuta le organizzazioni a capire quanto velocemente i loro team possono rispondere a guasti non programmati e quindi a identificare le aree che possono essere snellite all’interno di questi processi. Può anche aiutare a determinare lo stato di salute della risorsa stessa.
Misurare l’MTTR significa che le aziende hanno un metro di paragone per valutare come funzionano i programmi progettati per migliorare l’efficienza dei flussi di lavoro e dei processi dei tecnici. Un MTTR basso può indicare che sono necessari formazione o strumenti aggiuntivi. Può anche indicare che un asset critico si sta avvicinando alla fine della sua vita utile se l’MTTR aumenta improvvisamente rispetto ai livelli storici.
La formula per calcolare l’MTTR è: MTTR = tempo di manutenzione/numero di riparazioni.
Sebbene l’MTTR possa essere un KPI utile, è fondamentale valutare questa metrica in base alle circostanze specifiche di un particolare produttore o addirittura di un particolare dispositivo. Innanzitutto, è importante che i dati si basino su tecnici qualificati, che seguono procedure standard per la valutazione e la riparazione delle risorse. In secondo luogo, è utile tenere presente che ogni caso di guasto può variare notevolmente nel tempo necessario per la riparazione, da minuti a giorni o addirittura settimane. Poiché MTTR prende la media di tutti questi casi, potrebbe non essere altrettanto utile in un ambito più ampio. Invece, osservare una singola linea di produzione o una risorsa critica può aiutare a identificare meglio le aree di miglioramento.
Supponiamo che un produttore di petrolio e gas azioni una pompa che si guasta quattro volte nel corso di una settimana lavorativa di 40 ore e che impieghi rispettivamente 45, 30, 25 e 60 minuti per ripararla. L’MMTR viene calcolato sommando i minuti di manutenzione non pianificata, ovvero 160 minuti, e dividendolo per il numero totale di riparazioni, ovvero quattro. Pertanto, l’MMTR in questo esempio è 40 minuti.
Per ridurre questo MMTR, l’azienda potrebbe voler considerare la formazione fornita ai tecnici, gli strumenti e le informazioni giuste durante la riparazione e altri fattori che possono essere migliorati per aumentare l’efficienza. Nel corso del tempo, l’organizzazione potrebbe essere in grado di ridurre il proprio MMTR, migliorando la produttività e diminuendo i tempi di inattività totali non pianificati.
Planned Maintenance Percentage (Percentuale di manutenzione pianificata)
Il PMP misura la quantità di attività di manutenzione di un’azienda pianificata in anticipo, rivelando anche la percentuale di tempo dedicata alla manutenzione reattiva e di emergenza. Le migliori organizzazioni possono raggiungere un PMP superiore all’85%. Monitorando il PMP, i produttori possono identificare ulteriori opportunità per ridurre la manutenzione reattiva, misurare l’efficacia della formazione e degli strumenti e ridurre i costosi tempi di inattività non pianificati.
La formula per calcolare il PMP è: PMP = ore di manutenzione pianificate / ore di manutenzione totali x 100.
Asset Utilization (Utilizzo degli asset)
Misura l’utilizzo delle attrezzature negli scopi produttivi. Comprendendo quali apparecchiature non vengono utilizzate in modo ottimale, un’azienda può prendere decisioni informate sulle strategie di riallocazione o manutenzione che ne migliorano l’utilizzo.
Ad esempio, se una risorsa non viene completamente utilizzata su una linea di produzione, la prima domanda è: perché? Ordini insufficienti possono richiedere maggiori sforzi di vendita.? Un collo di bottiglia immediatamente prima di quell’asset può richiamare l’attenzione su quel punto di rallentamento? Oppure, ripetute richieste di manutenzione su quella macchina potrebbero indicare che è ora di sostituire o revisionare la risorsa stessa?
La formula per calcolare l’utilizzo delle risorse è: utilizzo delle risorse = 8.760 ore meno il numero di ore in cui una risorsa non viene utilizzata.
Preventive Maintenance Compliance (Conformità manutenzione preventiva).
La manutenzione preventiva viene solitamente eseguita dopo un certo periodo di tempo o di utilizzo; l’esempio più comune è un tipico cambio d’olio di un veicolo in base ai mesi o al chilometraggio. La manutenzione preventiva viene completata mentre la risorsa è ancora in funzione, nella speranza di ridurre le possibilità di guasti imprevisti.
La conformità PM misura la percentuale di ordini di lavoro preventivi programmati che vengono completati entro un tempo predeterminato. Le migliori aziende completano queste attività entro almeno il 10% dell’intervallo di manutenzione programmata. Ad esempio, le attività che devono essere eseguite ogni mese devono essere eseguite entro 3 giorni dalla data di manutenzione pianificata.
La formula per calcolare la conformità PM è: conformità PM = numero totale di PM completati/numero totale di PM pianificati x 100.
Conclusione
La selezione dei KPI giusti nella manutenzione può aiutare le aziende di un’ampia varietà di settori a migliorare l’efficienza, ridurre i tempi di inattività e contribuire ai profitti e alla redditività di un’azienda. Il primo passo, dopo aver impostato KPI e metriche di manutenzione efficaci, è capire come raccogliere dati di alta qualità per l’analisi. Avere i dati giusti aiuterà le organizzazioni a prendere decisioni aziendali più intelligenti sulla selezione delle aree di miglioramento con la massima priorità, nonché a misurare i progressi rispetto a tali miglioramenti futuri.
Concentrandosi sui KPI giusti che sono più strettamente legati agli obiettivi aziendali, i team di manutenzione possono illustrare meglio come il loro lavoro è legato ai ricavi, ai profitti e alla crescita complessiva. La gestione delle operazioni delle risorse enfatizza le decisioni aziendali basate sui dati e queste metriche di manutenzione possono aiutare la tua organizzazione a concentrarsi sulla riduzione dei tempi di inattività, sull’aumento della produttività e sulla riduzione al minimo dei tassi di guasto delle risorse. Tutti questi sforzi hanno un impatto diretto sui profitti.