Come ridurre i tempi di inattività nella produzione utilizzando un software CMMS
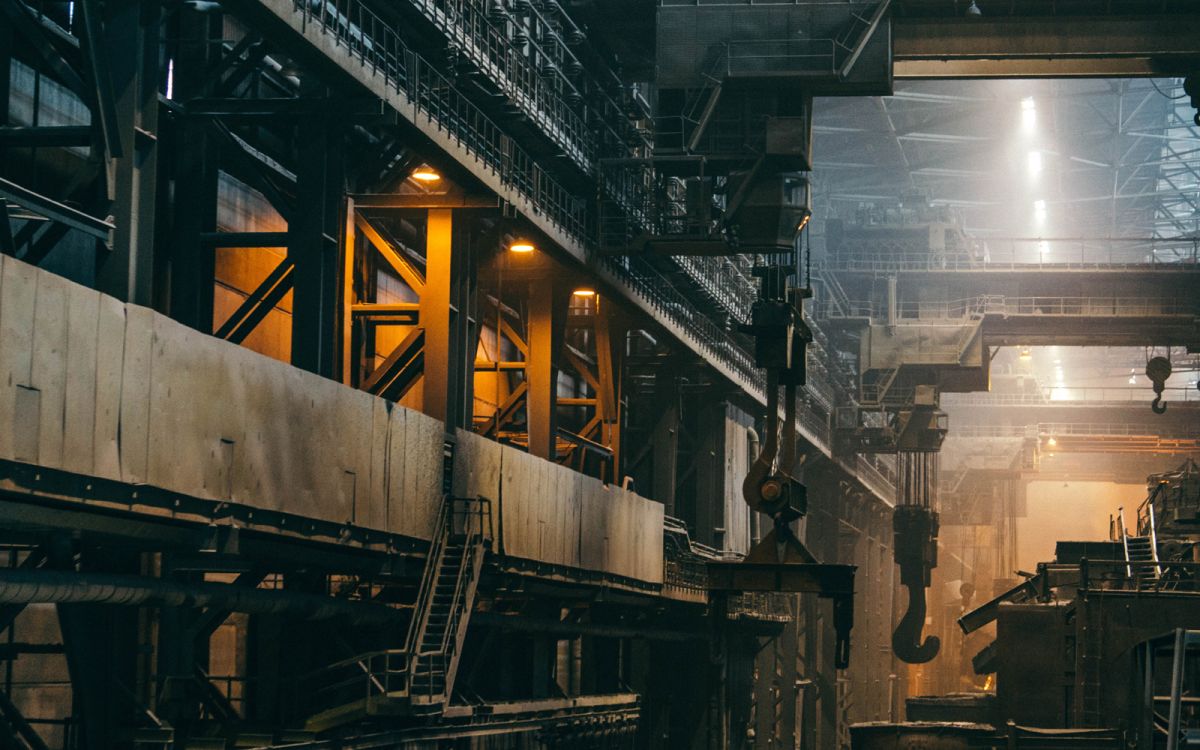
Gli asset che funzionano male creano aziende che funzionano male: è così semplice. Quando le organizzazioni affrontano costantemente problemi di manutenzione che comportano tempi di fermo della produzione, perdono tempo, denaro e altro ancora.
Ma i tempi di inattività non sono solo il risultato della rottura dei macchinari. Processi insufficienti, dipendenti scarsamente formati e privi di potere decisionale, pratiche inefficaci e altro ancora portano a tempi di inattività non pianificati che interrompono i processi e la produzione.
Scopri le cause più comuni dei tempi di inattività non pianificati nella produzione e come l’utilizzo di un software CMMS digitalizzato e centralizzato può offrire una serie di strategie di riduzione dei tempi di inattività che possono rappresentare un punto di svolta per la tua impresa.
Nel settore manifatturiero, le aziende registrano circa 800 ore di inattività ogni anno. Sentiamo spesso parlare di tempi di inattività non pianificati e di come influiscono negativamente su un’azienda, ma i produttori sperimentano due tipi di tempi di inattività durante i processi di produzione: tempi di inattività pianificati e non pianificati.
Sebbene si senta comunemente parlare di riduzione dei tempi di inattività non pianificati per aiutare la produzione, la pianificazione dei tempi di inattività pianificati potrebbe rappresentare un punto di svolta per la tua azienda.
Il tempo di inattività pianificato è un’interruzione che avviene di proposito. Spesso serve per implementare aggiornamenti, upgrade e modifiche alla configurazione che dovrebbero impedire il verificarsi di tempi di inattività non pianificati. Con questa manutenzione preventiva pianificata, le macchine e le applicazioni continuano a funzionare in modo ottimale per ridurre al minimo le interruzioni.
D’altro canto, i tempi di inattività non pianificati si verificano in modo imprevisto in qualsiasi momento. Di solito è distruttivo e comporta conseguenze in termini di produttività, entrate e altro ancora.
Che i tempi di inattività siano pianificati o non pianificati, hanno i loro costi:
- Entrate perse
- Costi di recupero
- Perdita di dati
- Costi di compensazione
- Produttività persa
- Danni alla reputazione
- Fidelizzazione dei clienti
1° Problema: processi degli ordini di lavoro inefficienti
Molte aziende trattano cinque tipologie principali di ordini di lavoro :
- Ordini di lavoro generali
- Ordini di lavoro di manutenzione preventiva
- Ordini di lavoro per ispezione
- Ordini di lavoro urgenti
- Ordini di lavoro di manutenzione correttiva
In genere, qualcuno all’interno dell’azienda (un operatore della macchina, un tecnico della manutenzione o qualcun altro) crea un ordine di lavoro identificando un’attività. Quando questo processo viene eseguito in modo inadeguato, senza informazioni adeguate o è incompleto in un passaggio o nell’altro, può portare rapidamente ad interruzioni all’interno dell’azienda.
Con un CMMS, gli utenti possono:
- Assegnare e dare priorità agli ordini di lavoro
- Esaminare le tendenze relative ai costi degli ordini di lavoro per ottimizzare il tempo, ridurre le spese di manutenzione, ridurre il tempo dedicato ai documenti, comprendere i dettagli in modo più chiaro e apportare modifiche più rapide.
- Ridurre i tempi di inattività delle apparecchiature garantendo l’affidabilità delle apparecchiature
- Aumentare il ROI delle risorse e aumentare la durata delle apparecchiature con la manutenzione preventiva
Le aziende non solo possono ridurre i tempi di inattività con la manutenzione preventiva, ma possono anche aumentare la produttività del team di manutenzione utilizzando un software di monitoraggio degli ordini di lavoro fruibile su mobile/smartphone per i tecnici che non stanno seduti davanti ad una scrivania.
2° Problema: dati inaffidabili e tenuta dei registri errata
Carta e penna sono ormai una cosa del passato quando si gestisce una impresa. Senza la digitalizzazione di documenti è difficile definire la proprietà del progetto e conservare i registri del lavoro per responsabilità. Nel complesso, questo porta ad attività di manutenzione incomplete che a loro volta portano a tempi di inattività inevitabili.
I registri digitalizzati garantiscono inoltre dati in tempo reale, affidabili e organizzati, facilmente accessibili per la revisione e l’analisi. Molto spesso, le attività di manutenzione non pianificate derivano da misure preventive inadeguate, che derivano da dati e registrazioni disorganizzati e inaffidabili.
Soluzione: analisi e reporting
Una sistema CMMS consente ai team di manutenzione di avere dati sotto controllo per ogni risorsa. Questa panoramica dei dati di facile accesso consente ai responsabili e ai tecnici della manutenzione di adattare il proprio approccio alla manutenzione preventiva.
La generazione digitale di report di manutenzione aiuterà a:
- Segnala questioni importanti
- Mantieni le riparazioni nei tempi previsti
- Mantieni responsabili i team di manutenzione
- Verifica che le riparazioni siano completate e monitorate
- Evita tempi di inattività non pianificati
- Aiuta a tenere il passo con l’inventario
3° Problema: pratiche di manutenzione inefficaci
La manutenzione programmata ha la sua importanza e può essere molto efficace se utilizzata correttamente. D’altro canto, pratiche di manutenzione inefficaci potrebbero essere dannose per la tua azienda. Quando le aziende utilizzano pratiche di manutenzione reattive vanno incontro a tempi di inattività non pianificati e a problemi spesso costosi.
Come fai a sapere se le tue pratiche di manutenzione sono inefficaci? Considera questi segnali:
- I tuoi tecnici stanno affrontando una grande quantità di lavoro non pianificato
- L’attrezzatura presenta continui malfunzionamenti e richiede riparazioni al di fuori della finestra di riparazione programmata
- I dipendenti stanno riscontrando un aumento dei tempi di inattività a causa della manutenzione non pianificata di beni e macchinari
- Si registra un aumento degli incidenti sul lavoro, soprattutto quelli causati dalle attrezzature .
- Il denaro speso per le attrezzature inizia a sfuggire al controllo.
Soluzione: manutenzione preventiva con un CMMS
Un sistema CMMS consente agli utenti di ripetere gli ordini di lavoro in base ai giorni, alle settimane o ai mesi trascorsi, per mantenere le apparecchiature in condizioni di funzionamento ottimali. L’attività di manutenzione preventiva può essere pianificata automaticamente in base alla data di completamento o all’intervallo di tempo assegnato a ciascuna attività.
Inoltre il software CMMS consente agli utenti di:
- Creare report di manutenzione
- Tenere traccia dei tempi di inattività e dei costi
- Gestire le risorse monitorando le soglie di quantità per le parti di ricambio
- E altro ancora
N° 4 Problema: monitoraggio dell’inventario insufficiente
Quando l’inventario non è reperibile o è esaurito, le riparazioni e la manutenzione pianificata subiscono notevoli ritardi.
Soluzione: mantenere parti e inventario
Il sistema di monitoraggio delle scorte di un CMMS ti garantisce in modo efficiente di avere tutte le parti necessarie per mantenere l’attrezzatura in funzione in modo fluido ed efficace. Puoi prendere il controllo del tuo inventario supervisionando tutto, dal consumo delle parti all’acquisto e altro ancora.
Non solo, non dovresti mai più rimanere a corto di inventario, ma con il software di controllo dell’inventario puoi anche:
- Creare codici a barre univoci per qualsiasi ricambio
- Evitare l’esaurimento delle scorte assegnando una quantità minima a ogni componente in modo da essere avvisato quando sta per esaurirsi
- Aggiornare automaticamente i conteggi dell’inventario man mano che le parti vengono aggiunte agli ordini di lavoro
- Ridurre i costi delle parti identificando i modelli nel tempo
- Conservare un registro storico di tutte le informazioni diagnostiche precedenti sulle parti
- Gestire l’inventario da qualsiasi luogo
5° Problema: dipendenti che non sono completamente formati e responsabilizzati
Secondi solo agli errori hardware, gli errori operativi sono la causa più comune di tempi di inattività. Uno studio del 2018 sulle centrali elettriche ha rilevato che il 56% dei guasti si è verificato meno di una settimana dopo un arresto programmato per manutenzione. Di questi guasti, il 55-65% erano legati alle prestazioni umane – errori operativi.
I dipendenti che non sono adeguatamente formati o che non hanno voce in capitolo quando sentono che qualcosa sta andando storto, potrebbero causare tempi di inattività imprevisti. Un buon operatore non solo rileva quando un asset mostra segni di errore, ma sa anche quando è il momento di sottoporlo a manutenzione. Un’adeguata formazione dei dipendenti insegna agli operatori a padroneggiare le attrezzature e potenzialmente a risolvere da soli i problemi relativi alle risorse, riducendo al minimo i tempi di inattività.
Soluzione: CMMS mobile semplice da usare
L’utilizzo di un CMMS mobile di facile utilizzo è una soluzione utile per i dipendenti. Non solo è possibile accedervi da qualsiasi luogo, ma richiede una formazione minima.
Un CMMS è specializzato nel rivoluzionare e razionalizzare processi di manutenzione e gestione delle strutture, al fine di gestire attività di manutenzione, risorse, ordini di lavoro, gestione dell’inventario e molto altro ancora.
Quando i dipendenti sono coinvolti nei processi importanti, è utile promuovere strategie di manutenzione proattive per migliorare l’efficienza operativa e ridurre i tempi di inattività.
Conclusione
I tempi di inattività nei processi di manutenzione sono un problema che quasi tutte le organizzazioni si trovano ad affrontare. Che si tratti di guasti alle apparecchiature, gestione inefficiente degli ordini di lavoro, mancanza di trasparenza tra i lavoratori o assenza di un processo decisionale basato sui dati, i tempi di inattività comportano perdite di tempo e denaro.
Un sistema CMMS trasforma il modo in cui le aziende affrontano la riduzione dei tempi di inattività. Digitalizzando le attività di manutenzione, gli ordini di lavoro, il monitoraggio delle risorse, l’analisi dei dati e altro ancora, le organizzazioni possono migliorare l’efficienza e ridurre i costosi tempi di inattività.