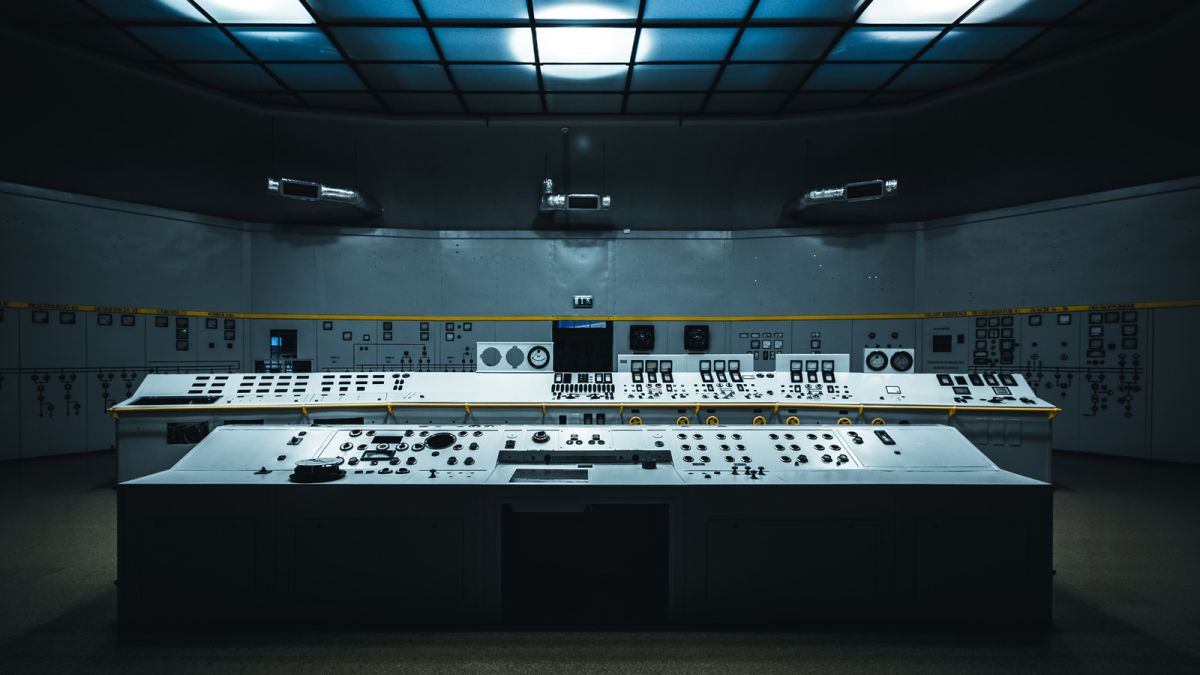
Oggi la concorrenza nel settore manifatturiero è spietata e i tempi di inattività possono rappresentare un incubo molto costoso. Che tu stia producendo componenti automobilistici, imballando beni di consumo o gestendo una flotta di veicoli, i tempi di inattività significano perdite di entrate, produttività ridotta e il rischio di compromettere le relazioni con i clienti. Per ridurre i tempi di inattività, le aziende devono trovare modi per misurarli e implementare strategie di manutenzione sia preventiva che predittiva.
Che cosa sono i tempi di inattività?
Quando parliamo di tempi di inattività, ci riferiamo a qualsiasi periodo di tempo in cui un’apparecchiatura, una linea di produzione o un intero sistema non funziona come dovrebbe. Ciò include sia i tempi di inattività pianificati che quelli non pianificati.
I tempi di inattività pianificati vengono organizzati in anticipo per la manutenzione, aggiornamenti o altre attività. Anche se previsti, i tempi di inattività pianificati devono comunque essere gestiti attentamente per ridurre al minimo il loro impatto sulla produttività complessiva.
I tempi di inattività non pianificati sono molto più dannosi per un’organizzazione perché si verificano inaspettatamente. Può essere causato da guasti alle apparecchiature, guasti o altri eventi imprevisti, causando interruzioni immediate e perdite finanziarie.
Sebbene i tempi di inattività pianificati mettano offline una risorsa, non dovrebbero influire su altri processi di produzione o sul personale. I tempi di inattività non pianificati, d’altro canto, possono avere un effetto domino, causando un collo di bottiglia in un processo di produzione o lasciando i lavoratori di linea senza nulla da fare, aumentando le perdite ad essi associate.
Monitoraggio dei tempi di inattività
Come dice il vecchio proverbio: “Non puoi migliorare ciò che non misuri”. Il primo passo per aumentare i tempi di attività è monitorare i tempi di inattività. Fortunatamente, oggi esistono molte tecnologie e strumenti diversi per aiutare le aziende a farlo in modo efficace.
Innanzitutto, i produttori devono implementare un sistema per raccogliere dati accurati. Informazioni come quando si è verificato il tempo di inattività, quanto è durato e quali sono state effettivamente le cause profonde sono fondamentali per le misurazioni della qualità. I sistemi computerizzati di gestione della manutenzione (CMMS) possono fungere da archivio di dati se i tecnici sono adeguatamente formati per inserire le informazioni. Inoltre, molte aziende possono trarre vantaggio dall’utilizzo di sensori Internet of Things (IoT) in grado di automatizzare la raccolta dei dati.
In secondo luogo, un’organizzazione deve disporre di un modo efficace per generare report sui tempi di inattività ed eseguire l’analisi dei dati in modo da poter identificare modelli ricorrenti. Questi report possono indirizzare i team di manutenzione verso macchine specifiche che sembrano più soggette a tempi di inattività o attività particolari che sembrano essere costantemente ritardate.
Implementazione della manutenzione preventiva
La manutenzione preventiva è un approccio proattivo che mira a prevenire guasti alle apparecchiature e ridurre i tempi di inattività non pianificati. Ogni azienda deve considerare quali aspetti della manutenzione preventiva genereranno il massimo ritorno sull’investimento e stabilire le priorità di conseguenza. Ecco alcuni potenziali componenti della manutenzione preventiva da considerare:
- Gestione delle risorse: crea un elenco completo delle risorse e classifica ciascuna risorsa in base alla sua criticità per le tue operazioni. Ad esempio, alcune macchine possono essere fondamentali per rispettare le scadenze di produzione, mentre altre non svolgono un ruolo così importante. Dare priorità agli interventi di manutenzione preventiva sugli asset ad alta criticità dovrebbe ridurre maggiormente i tempi di inattività.
- Pianificazione della manutenzione : sviluppa un programma di manutenzione basato sulle raccomandazioni del produttore, sulle migliori pratiche del settore e sui dati storici, sui tempi di inattività. Ad esempio, se noti che i cuscinetti di un particolare asset tendono a guastarsi ogni 10 mesi, potresti voler programmare la sostituzione ogni otto-nove mesi per evitare tale guasto.
- Manutenzione predittiva : la tecnologia dei sensori ha fatto molta strada negli ultimi anni. Ora i sensori possono monitorare vibrazioni, temperatura, livelli dell’acqua, umidità e altro ancora su base quasi costante. Inoltre, molti possono essere programmati per inviare avvisi automatici quando le prestazioni scendono da un intervallo accettabile, indicando un guasto imminente. Utilizzando queste tecnologie per monitorare lo stato delle tue macchine, puoi “individuare” potenziali guasti appena in tempo.
- Inventario dei pezzi di ricambio : tenere un inventario eccessivo può comportare costi più elevati per tracciare e archiviare gli articoli, nonché sprechi se gli articoli scadono o diventano obsoleti. Tenere un inventario insufficiente, d’altro canto, può significare tempi di inattività aggiuntivi o costi di spedizione accelerati quando un bene necessita di riparazione. Può essere utile tenere traccia dei dati, ad esempio quali pezzi di ricambio sono critici, potrebbero richiedere tempi di consegna più lunghi o si prevede che saranno necessari nel prossimo futuro.
- Formazione e sviluppo delle competenze : assicurati che i tuoi tecnici non siano solo formati per diagnosticare i problemi in modo rapido e corretto, ma anche per registrare correttamente i dati per futuri lavori di analisi e manutenzione. Ciò può richiedere un cambiamento culturale, instillando l’importanza di far lavorare tutti insieme per garantire che siano disponibili informazioni accurate e complete.
- Analisi della causa principale : ogni volta che si verificano inevitabilmente tempi di inattività, condurre un’analisi approfondita della causa principale, in particolare sulle risorse più critiche. Risolvere solo il problema immediato non farà altro che ritardare riparazioni più permanenti e a lungo termine, il che aumenterà costi, problemi e frustrazioni per tutti. Lavora per identificare i problemi sottostanti e implementare azioni correttive per prevenire eventi futuri.
- Miglioramento continuo : come ogni programma di successo, è fondamentale rivedere e perfezionare regolarmente il programma di manutenzione preventiva. Prenditi il tempo necessario per considerare le lezioni apprese dagli incidenti legati ai tempi di inattività, dalla ricerca sulle cause e da altri incidenti passati per apportare miglioramenti sia alla tecnologia che ai processi di lavoro per fare meglio in futuro.
Conclusione
I tempi di inattività sono forse uno dei problemi più costosi che un produttore può affrontare. Monitorando i tempi di inattività attraverso una raccolta dati accurata e completa, insieme all’implementazione di un solido programma di manutenzione preventiva, le organizzazioni possono ridurre le interruzioni non pianificate, migliorare l’affidabilità delle apparecchiature e, in definitiva, massimizzare il tempo di attività delle risorse critiche. Alla fine, quel livello di migliore efficienza operativa significa costi inferiori, meno frustrazione, maggiori profitti e clienti più soddisfatti.